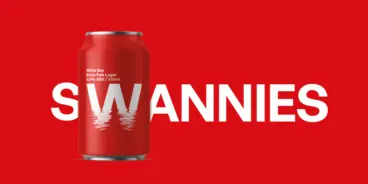
Automated forecasting is a "game changer" for stocktake
With End of Financial Year (EOFY) 2022 approaching, now is the perfect time to get a game plan in place for proper tracking of raw materials, packaging supplies, and other items for your 2023 Financial Year. At The 5th Ingredient, we realize that SOFY (Start of Financial Year) planning goes beyond just doing a stocktake. So we decided to talk more about the benefits of a function just as important – Material Resource Planning (MRP), and how it can save your business thousands of dollars annually.
Chances are you’ve heard about material resource planning (MRP). For those who haven’t, MRP is a game changer! It works by taking a brewery’s current inventory, all planned purchase orders, and all planned production, then based on the recipes for planned production, it automatically calculates future inventory for all raw materials and packaging items. From there, it automatically creates suggested purchase orders based on item lead times. In short, material resource planning takes one hundred percent of the effort out of the process of figuring out when brewers need to buy things to hit production.
Why is MRP important?
Because automated inventory forecasting and suggested orders makes it simple to prevent running out of either raw materials or packaging supplies. This can help you avoid an array of bad outcomes such as running out of either raw materials or packaging supplies. Keep reading to find out more.
Loss of Income
This one may seem obvious, but each day that you’re out of a finished product that is in high demand by your accounts or distributors, is another day of lost revenue. A loss of income spirals further out, if, while out of product, shelf/cooler space and/or tap handle placements at bars and retailers are replaced with competitive brewery brands.
The landscape is so competitive right now that retailers won’t deal with empty shelves. Especially large retailers like grocery stores and liquor chains. There’s a chance they will replace your brewery’s products with competitive products despite your product being in demand. Further costs can then be incurred as your sales and marketing teams have to win back placements that used to belong to you.
Increased Shipping Costs
Failure to properly plan and forecast production can lead to increased shipping costs as you have to expedite shipping. Simply put, faster shipping costs more. Further costs could be incurred as improperly forecasted orders can cause brewers to have to order partial pallets and partial container loads of raw materials.
Inconsistent Brews
Quality loss and inconsistencies can occur if the incorrect raw materials are on hand. Instead of halting production until the correct materials are on hand, a brewery may decide to substitute ingredients in. This could sacrifice recipe quality or create inconsistencies from batch to batch.
There can also be a secondary level of fallout on a personal level as your wholesale customer and retail accounts trust you less to be able to provide product consistently. Your operations team can also suffer from frustration as scheduling delays, cancellations, and other inefficiencies occur.
As soon as you lose the trust of the quality of your beer, you’re dealing with an uphill battle to regain that trust – which could have been prevented if you had the proper raw materials in the first place!
The Importance of MRP from a Former Brewery Production Manager
Dave Short is a Customer Experience Specialist with The 5th Ingredient. Formerly Dave was Brewmaster and Production Manager with 49th State Brewing Company in Anchorage, AK. Here is Dave’s experience with material resource planning:
“As the production manager it was really all about keeping us on schedule and just maximizing the amount of beer we could put out. I had two brew pubs and we were building out a third production facility. We actually had, not only the busiest brewpub in the state, but the busiest restaurant in the state of Alaska. So we went through a massive amount of draft beer just at one of our locations and quite a bit at our second location as well.”
“We couldn’t really afford to make any mistakes.”
“And by mistakes I mean like running out of ingredients or raw materials. Not only did this include items like grains, hops, or adjuncts, but also bottles, bottle caps, brand specific labels for our brands. If we had one minor slip up in the summer it would cause us to be out of a beer on the shelves. And that was a major, major problem because it was an income loss for us.”
“MRP was the whole driving force for our brewery to go with brewery software.”
“Having an MRP tool like what Beer30 offers is such a massive time-saver. For starters, fewer mistakes are made. But it also makes all the information available in one place versus having to collect hand counts and trying to map them up with my purchase orders, then looking separately in the brew schedule, and trying to create Gantt charts. I did all of that manually and was learning to be successful at it, but it was a challenge.”
“Don’t Let Inventory Keep You Up at Night”
Zach Volkman is the Head of Revenue Operations for The 5th Ingredient. Formerly Zach was Chief Operating Officer of O’Connor Brewing Company in Norfolk, VA, and prior to that, was a Process Engineer at Ballast Point Brewing, in San Diego, CA.
“At my previous job, I ran our purchasing of packaging materials for about six months, using nothing other than spreadsheets and a Google calendar. At the time, we were bottling, canning and kegging five days a week.
I would say, at times, I was spending at least 10 hours a week manually calculating and trying to forecast out exactly what my consumption rate was going to be on every single item. Then I was trying to stay ahead of four to eight week lead times, especially for printed boxes and items like that. Not to mention, we’re trying to buy it in bulk to hit price points.”
“I think I legitimately had nightmares about shutting down the entire production operation because we were missing an item.”
“And then all of a sudden you’re tying up a bright tank. You can’t even necessarily filter the next beer or switch to something else. From there, it’s just a cascading effect that could be a total headache. I couldn’t agree more that MRP was a huge motivation to go for craft brewery software. One thing I like most about Beer30 is that it has a lead time feature with suggested purchase orders.”
Tips for Using MRP Successfully
When used correctly, the MRP tool in Beer30 can be a major game-changer for your brewery. It’s important to keep in mind that MRP is only as good as a couple of things. It’s as good as your real inventory count, production plan and as your lead time from your vendors. Therefore it’s important to do the following for accurate results:
- Get a good inventory count.
- Plan your production out as far as you possibly can.
- Get your vendors to commit to a lead time.
The Beer30 MRP Difference
Beer30 was built for brewers by brewers. Due to our team’s decades of experience in the brewing industry, we know firsthand the pain points breweries face with inventory management. So, when designing Beer30’s MRP features it was important for us to address those issues.
One thing that sets our MRP module apart is the fact that brewer’s have the recipe in Beer30 and can easily track substitutions. This helps breweries keep their inventory accurate and remain prepared. In addition, another big one that helps MRP run smoothly with Beer30 is that cellar activities are also included within the recipe. So any dry hopping, cellar additions, adjuncts like pineapple or mangoes, cold side changes, or packaging gets factored in as well. Last but not least, Beer30 offers suggestive ordering by automatically calculating when and how much of an item to purchase.
Brew Better with Beer30
Well, with all that said, you can now do your inventory stocktake done in Beer30 for the new 2023 Financial Year. There are currently 1 in 7 breweries in Australia using Beer30 for their brewery operations. Beer30 makes it easy to track the onslaught of data you need to keep track of on an everyday basis. We’re not just talking about brewing ingredients like grains, hops, yeast, and adjuncts.
With Beer30, you’ll always be up to date on packaging materials, including cans, bottles, crowlers, growlers, kegs, and labels, and know where you stand, not only with finished products, but the beers fermenting in your cellar. Beer30 gives users crystal-clear visibility over work-in-process products in tanks. We currently have an EOFY / SOFY promotion for new Australian customers: get 20% off your first 3 months using Beer30, if you sign up by July 15, 2022.