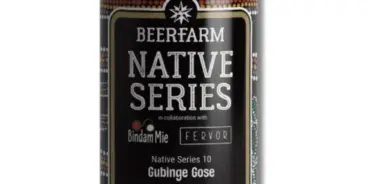
Barrett Burston's wastewater recycling saves 1bn litres
As brewers begin to look more closely at their wastewater and how to reuse or treat it, Barrett Burston Malting has achieved a major milestone following the implementation of wastewater recycling technology, having now saved 1 billion litres of water.
Barrett Burston has been working with engineers at Permeate Partners to resolve issues with a wastewater recycling system which was installed a decade ago, and as a result of this work has saved more than 1 gigalitre of water by recycling water from its barley processing facility.
Water usage in breweries and associated industries has been a key issue for brewers as they focus on sustainability throughout their operations.
Some breweries globally have made headlines for brewing beer out of wastewater. In Australia, breweries have been working with new technologies to reuse their wastewater, with startups such as SwitcH2 which intends to turn wastewater into fuel through an electrolysis technique, which is currently being trialled at Jervis Bay Brewing Co. in NSW.
But brewers can also learn from much larger scale projects dealing with wastewater and water recycling, such as that at Barrett Burston, or Lion, which invested in a reverse osmosis plant which reuses waste water, enabling a litre of XXXX Gold to be produced with 2.8 litres of water.
Since then, smaller breweries such as Rocky Ridge have managed to reduce their water usage ratios to similar ranges through a variety of methods.
Wastewater is a big issue as well to breweries working out with their local authorities what to do with it and how much it will cost to treat it.
Paul Malone, plant manager at Barrett Burston Maltings, said that the recycled water component of the wastewater treatment plant is quite complex.
“It involves removing suspended solids from the effluent, passing the waste water through a series of membranes and then a reverse osmosis plant.
“There is pH correction and microbial treatment using chlorine dioxide to enable us to re-use this water as ‘potable’ water in our process. This technology is quite common though and certainly can be scaled down,” Malone explained.
Hear more about Rocky Ridge’s sustainability progress on the Beer is a Conversation podcast with co-founder Hamish Coates.
Water reuse on a small and large scale
Barrett Burston was part-funded in 2009 by Geelong City Council to implement water savings projects, so it chose to install the waste water treatment plant to reduce water being taken from municipal storage and to improve the quality of effluent being discharged into the sewer.
While Malone was not on board back then, he said their values then would no doubt be similar to those today.
“BBM were very keen to commit to this investment as the costs for sending untreated effluent to local water authorities, combined with large volumes, is a huge cost to the business.
“Purchasing water is not that expensive in comparison, but I’m sure BBM wanted to be seen as helping with water conservation at what was a pretty bleak time for the State water storages,” he said.
To ensure that the system was working at optimum levels, Barret Buston brought in Permeate Partners a few years ago, and now the plant recovers on average up to 12 million litres of water a month.
“This volume would have been previously sent to the sewer, but also we would be purchasing the equivalent volume of water from the ‘town’ water authority. We now are sending, on average, 4 million litres a month to trade waste sewers.”
Whilst this technology is not new, with wastewater treatment plants in place in other industries for decades, in the world of brewing it is much less common – but things are changing.
The costs of sending wastewater to municipal centres versus investing in and paying the energy bill for a wastewater plant may be comparable in the short term, but there are also other reasons for investing, according to Permeate Partners’ technical manager Peter Gordon.
“Biological processes are inherently energy intensive processes, around aeration in the biological system to keep the biomass which is breaking down the organics and you have to have a certain level of DO [dissolved oxygen] for that. In BBM they have surface aerators which are constantly mixing up the water and aerating it.
“But the reality is if it didn’t happen there it would be pumped to a wastewater treatment site where they would need to follow the same process to break it down pretty much, so the energy saved would be localised,” Gordon explained.
“You’re really saving those transfer all costs, because they need to move it long distances to be treated, then there’s the probability it will be discharged to the ocean. Short-circuiting that and treating it locally, the savings are transfer of the waste water.
“We promote local treatment and local use – you’re saving the transfer of liquids over long distances there and back when you bring that potable water back in as well.”
While the Barrett Burston project was a relatively large one, the technology is scalable, explained Gordon.
“In principle the tech is exactly the same but looks different, and the approach is similar,” he said.
“But it is a biological process which takes up floor space, there is a required hydraulic retention time for the breakdown of the biological matter in the wastewater, that’s what takes up most of the space
“But we can do it in the compact form. How [Barrett Burston] chose to approach the design meant that the biological process is more a lagoon or a pond, but you can do it in deeper tanks and make it more compact, so it can be hard to define the footprint.
“[In this case], Barrett Burston could have shut it down when it wasn’t working well but they saw the benefit from an environmental perspective and made sure it did.”
pH Correction in wastewater
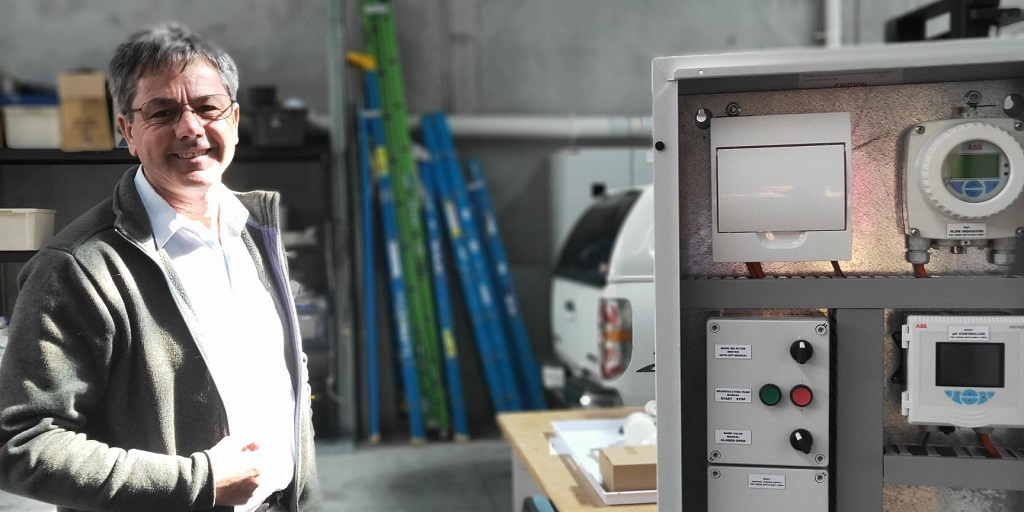
Cromarty director Richard Grant at Deep South Brewing with its new pH correction unit
Elsewhere, brewers might not be able to invest in full water reuse and recycle systems, but they can make a difference in the quality of the water they direct to municipal systems.
Engineering specialists Cromarty have worked with brewers including Spotty Dog Brewers and Deep South Brewing Co. in Tasmania in the development of a pH correction system for brewery wastewater.
“The water authorities test water down here for commercial customers and it has to be within a certain range. This has to be recorded by calibrated instrumentation,” explained Cromarty technical solutions coordinator Sam Gibson.
“Authorities like the water pH to close to 7 so it’s neutral, otherwise it makes it difficult to treat wastewater.
“It’s going to be problematic to treat in the treatment plant because ultimately, the worst of the effluent is, the more you have to spend to fix it.
“So if the pH is incorrect, they actually have to dose that water with other chemicals to balance it, and those chemicals are really expensive. So that’s why commercial customers always get charged – it’s expensive generally to dispose of trade waste.
“But if you can then get systems implemented cost effectively where you can correct trade waste, you can start to prove that you’re treating the stuff that you’re pushing out of your facilities.”
Cromarty has developed an automated pH correction system for smaller breweries which uses a recirculation pump to keep the liquid mixed all the time so its pH level can be tested, and is connected to a dosing pump of caustic acid to ensure the water is dosed back into a good pH range. It is then dumped out and measured using a magnetic flow metre to monitor the total trade waste for reporting back to the utility with the corresponding pH when dumped.
“pH model monitoring and correction has been around forever. So from a water utility perspective, they’re very comfortable with this approach. It’s not like we’re actually coming up with something that’s not industry standard, it’s a very well-proven technology.
“The art is providing an automated solution which fits into the budget of most brewers because they don’t want to spend a million of dollars on these sorts of systems whilst also appeasing the utilities requirements.
“I think the biggest element is probably education, and it’s that education around, hey, there’s actually a really cost effective solution out there, I don’t have to go a country mile, I can actually pick what I want, and maybe just want to monitor my pH if I don’t want to correct it.”
Additionally, the key element of this technology is the data that can be collected.
“We are monitoringflow and pHwhich is thenrecorded bythe client, butcanalso reportdirectly tothe utility. So they can both independently track what trade waste going out is to then say, hey, we’ve got a problem here, guys, your trade waste pH is too high.
“And the brewing industry is an important thing to utilities companies, you know, five or 10 brewers putting lots of lots of untreated waste into the system is a big, big environmental load on utilities.”
How are you treating or recycling your wastewater in the brewery? Let us know clare@brewsnews.com.au.