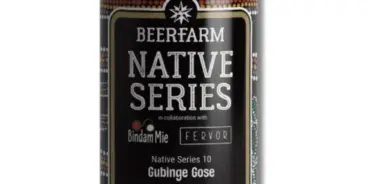
A single solution for monitoring beer quality
Quality can determine the success or failure of any product, in our case beer. With ever more beverages on the market, consumers are more knowledgeable and attentive to the products they choose, what they contain and how they are prepared. Developments in legislation relating to beverage contents and labelling have also contributed to this new awareness.
To facilitate beer quality control processes, it is necessary that the source materials themselves are of the highest quality.
At CFT we have developed a tailor-made solution ideal for all brewers, and beverage producers in general, who wish to monitor product quality to ensure product excellence.
This is a quality analysis system, the “QA Module” (Quality Analysis), which allows for online and continual control over the physical and chemical characteristics that beer must possess to be considered high quality.
The CFT control system for beer quality: The advantages
Continuous, precise and consistent monitoring
Brewers often have specific instruments for monitoring and measuring, which are installed on the different machines that make up the line. This strategy of monitoring beer characteristics brings with it risks of inconsistent data, related to the gap between the instruments themselves, which prevents a systematic, integrated and reliable reading. The alternative of analyzing beer in the laboratory is also fraught with risks: the possible contamination of samples and an analysis time that prevents prompt intervention in the event of problems.
The CFT module is a single unit, with the advantage of having all the parameters that determine product quality located in a specific area of the plant, reducing the risk of inconsistent data readings and contamination of product samples.
Hygienic and compact design
The CFT beer quality analysis module is extremely compact and constructed entirely of stainless steel. The skid’s unique design and advanced hydraulic features meet the highest hygienic design standards (EHEDG regulations – European Hygienic Engineering and Design Group). Its compact nature and simple installation allows it to be incorporated into existing installations, adapting to even the most complex of layouts.
Versatility and high instrumentation quality
This unit is extremely versatile and can be designed according to the specific requirements at each customer’s plant. Usually positioned between the fermenters and the filler, it can be placed on separate pipelines to feed several lines simultaneously. The instrumentation installed within the unit is carefully sourced from selected suppliers to ensure the highest levels of quality. The choice of instrumentation itself is flexible.
Ease of use and digital interface that can be intergrated
The Beer QA Module is easy to use and is equipped with a digital interface that can be integrated into any existing supervisory systems in the plant. This makes it possible to monitor product quality without interruption, providing a constant flow of data to the supervision system, which processes it to obtain valuable insights.
An example of a supervision system that can be integrated into the QA module is Memento, developed by CFT for all its packaging machines.
Features of the beer quality control system
Among the main features of the beer quality analysis system we can mention:
- An optical verification unit for the product in transit
- A drainage system (in case the product is out of specification)
- A basket filter
- A mass flow meter (with densimetric reading)
- Sampling unit
- A Ph reading unit
- A conductivity meter
- An oximeter unit
- A pressure transmitter for fermenter pump management
- A multi-way plate for flow management
QA Module: Maximum quality assurance for all beverages
The product quality analysis module, typically applied to beer but also suitable for other types of beverages, is a bespoke solution that guarantees quality and safety. The ease of installation and the possibility of integration with other supervision software makes it a suitable solution for many companies in the beverage industry, as well as a valid added value for continuous production monitoring. If we add to this a market trend that increasingly leads consumers to prefer premium category beverages, thanks to continuous innovation in taste, flavour and packaging, it is clear that building a culture of quality is essential at every level of the supply chain.
Sources:
https://www.alliedmarketresearch.com/
About CFT Group
CFT Group’s history begins in 1945, from the idea of the entrepreneur Camillo Catelli who started to produce machines for the tomato processing industry in a small factory in Parma, Italy.
Today CFT Group designs and manufactures machineries and complete turn-key lines for the processing and packaging of Food & Beverage products. Since 2021, the company has been part of ATS Corporation, a world leader in industrial automation. ATS and CFT work in synergy to offer increasingly cutting-edge solutions for the Food & Beverage Industry.
CFT Group will participate in Brewcon 2023 with three companies, that are all part of the Group: CFT, Comac and Rolec. Rolec specializes in equipment for beer production; Comac designs and manufactures low capacity fillers for kegs, cans and bottles; CFT specializes in high capacity fillers for cans and bottles (ideally up to 40-50.000 cph) + end of line technologies (robotic pals & depals, also for kegs). In the last twenty years, the three companies together collected one thousand of references in the beer industry, from pub-breweries up to international companies with high capacity lines.